The U.S. Army’s Jointless Hull project is developing the world’s largest metal 3D printer, capable of repairing or printing large vehicles up to 30 feet long, 20 feet wide and 12 feet high. The 3D printing technology at the heart of this collaborative project is a solid-state metal process pioneered by Meld Manufacturing. The Christiansburg, Virginia-based company provides 3D printing equipment for an additive version of the friction stir welding process, which welds metals without melting them. Its offerings include three different standard machines (the L3, K2 and 3P) as well as the CD-14 package of a spindle with rotating deposition tool, electrical enclosure and HMI, suitable for large, custom systems like the Jointless Hull machine.
As the technology has evolved to serve these different needs, Meld has found that open, scalable control technologies are critical to enabling continued development. Its machines today use flexible EtherCAT and PC-based automation for control; hardware and software from Beckhoff Automation have allowed the company to improve user experience, simplify commissioning and integration, and continue to evolve the platform.
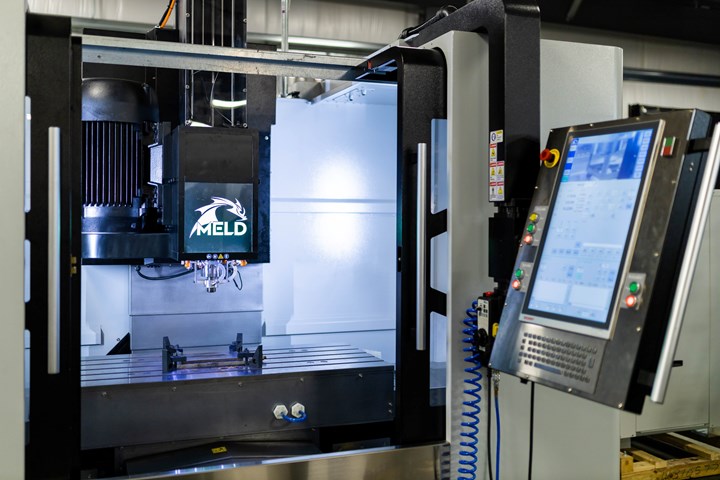
A Meld Manufacturing machine is prepped and ready to print. The company’s friction stir welding 3D printers use EtherCAT and PC-based automation from Beckhoff. Photo Credit: Beckhoff / Foreword LLC
Additive Manufacturing Based on Friction Stir Welding
Led by CEO Nanci Hardwick, Meld Manufacturing spun off from its parent company, Aeroprobe, in 2018 to apply its additive friction stir deposition to additive manufacturing technologies. Friction stir welding is a method for welding metals without melting them that gained traction among aerospace companies in the 1990s. Meld developed a similar, but unique additive process to enable deposition of multiple layers for 3D printing applications. The process entails rotating a bar of solid metal while applying a specified force at the point of deposition. Friction causes the metal to plasticly deform and be deposited in a layer. Through adiabatic heating, the metal feedstock will continue to flow if spun continuously at the correct speed.
The Meld process welds layers of material together without melting them, producing strong metal parts. Photo Credit: Beckhoff / Foreword LLC
The Meld process allows equipment end users to print parts using any metal, including aluminum alloys and others that have typically posed problems for other additive manufacturing systems. It also doesn’t require melting like most other methods and thus doesn’t affect the metals’ properties. As a result, the product remains stronger than parts made through other metal 3D printing or even traditional forging processes. Unlike melt-based metal additive processes, Meld-made parts are not susceptible to porosity, hot-cracking or other typical issues. The process is also faster than fusion-based metal additive processes and requires less energy.
Today Meld offers its process to a wide range of customers in defense, research and manufacturing. Its standalone machines accommodate part sizes ranging from 3 feet long and 1 foot tall to roughly 13 feet long and 3.5 feet tall. Open, scalable industrial control technologies have proven critical to enabling continued development.
“Every time we learn something new in our engineering, we need to adapt the machines,” says Dr. Fred Lalande, senior automation engineer at Meld. “So the automation technologies we use must be very flexible.”
After the company launched in 2018, its original controls platform could not keep pace. First, Lalande had difficulty getting the controller to use G code for printing; he had to write a G code interpreter for that vendor’s platform. A separate PC using a separate software package was also necessary to run the HMI and communicate performance data. Finally, the platform had difficulty connecting field devices. As Lalande worked to make the platform communicate to a Beckhoff stepper motor terminal, he got in touch with members of the local Beckhoff team regional sales engineer Chuck Padvorac and application engineer Jack Plyler.
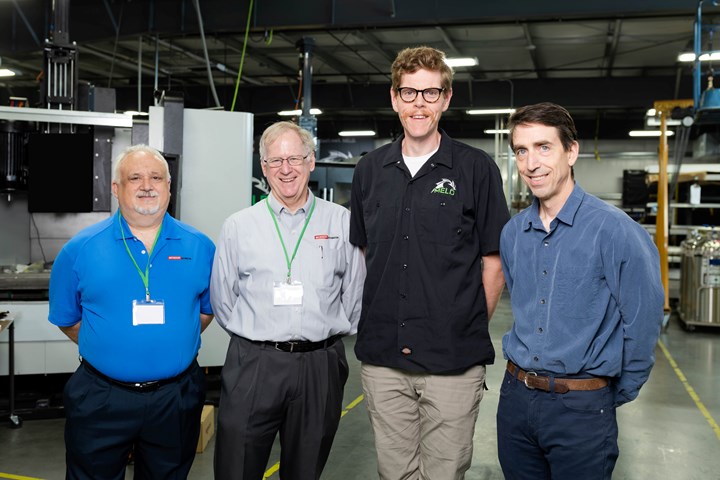
At the Meld Manufacturing facility in Christiansburg, Virginia (from left): Jack Plyler and Chuck Padvorac of Beckhoff meet with Chase Cox and Fred Lalande of Meld. Photo Credit: Beckhoff / Foreword LLC
The Beckhoff engineers visited Meld to assist Lalande with the integration. As he learned about fully integrated PC-based control from Beckhoff, Lalande believed he had found a suitable platform for Meld’s developments. “Our technology evolves so quickly that it can be challenging to anticipate all future needs, but it was clear that Beckhoff and its TwinCAT software offered a platform that would not constrain us,” he explains. “It was also important for us to have a very open system with a wide range of available hardware. With EtherCAT, we can select from countless I/O terminals and field devices — from Beckhoff or third parties — to cover the gamut of functions we might need.”
PC-Based Automation Simplifies Programming and Integration
What pushed Lalande toward Beckhoff was TwinCAT 3 automation software. TwinCAT provides an end-to-end engineering and runtime platform for everything from PLC, CNC and motion control to HMI, machine vision, IoT and more. The software enables programming in any of the available IEC 61131-3 languages including object-oriented extensions, function blocks and computer science standards in Microsoft Visual Studio. Since Lalande had programmed the first machine’s code in structured text using CODESYS, he found it relatively easy to convert the code in a short timeframe. He not only implemented a program that can execute G code files within the PLC using the TwinCAT NCI package, but he also designed a new HTML5-based operator interface in TwinCAT HMI.
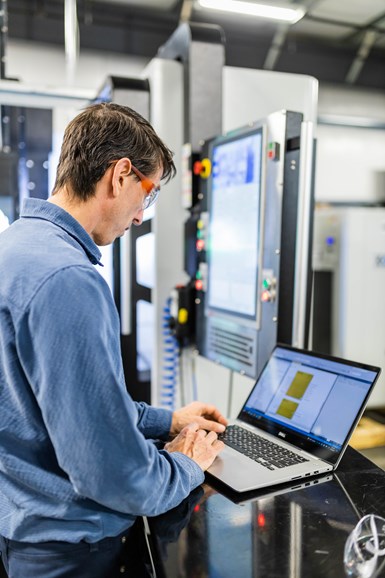
TwinCAT 3 provides a flexible engineering and runtime platform that enables continuous development of Meld technologies. Photo Credit: Beckhoff / Foreword LLC
“Previously, I had to use two or three different software packages. That was a pain,” he says. “With TwinCAT, I open one program and everything I need is there.”
As the Meld solutions have developed, the code has grown more sophisticated. The portability of code in TwinCAT made it easy to adapt one machine’s program when designing the next. It also helps to ensure quality in each print. The spindle speed must be modulated for each specific material to maintain the desired temperature for continuous printing, explains Dr. Chase Cox, director of technology at Meld:
“Given how far the tool has moved, we know from our development how much material should also be delivered,” he says. “We ensure the incoming material deposition rate is correct using Beckhoff systems to control that velocity profile.” To accomplish this, the PID controller in the TwinCAT Controller Toolbox provides dual-loop closure on the axis.
In addition, TwinCAT also provided advantages in IP protection. As Padvorac points out: “The Beckhoff software platform gave Meld the ability, using our OEM Certificate feature, to lock down its valuable code. Everything is password protected and encrypted, so no one can copy Meld’s developments.”
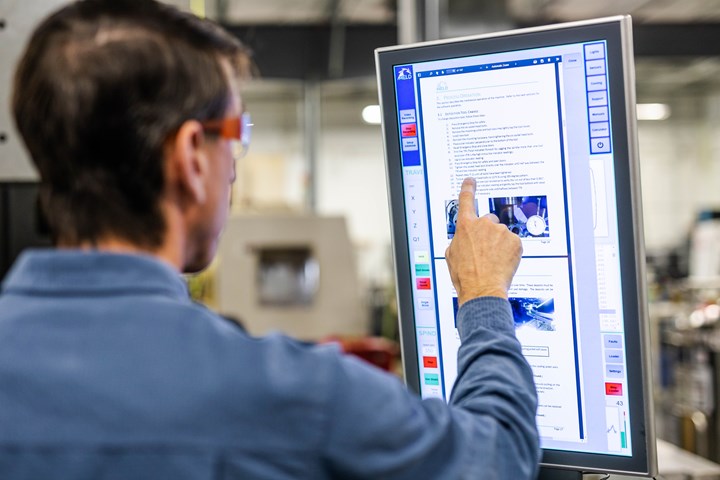
Beckhoff multitouch control panels and TwinCAT HMI allow for an intuitive operator interface with web-based programming. Photo Credit: Beckhoff / Foreword LLC
For each Meld machine, the TwinCAT program runs on a single Beckhoff C6920 control cabinet Industrial PC (IPC). This allowed the engineering team to eliminate the other PC, saving cost and space in the machines. A CP2924 multi-touch control panel from Beckhoff provides the operator interface with custom push-button extensions. The K2 machine features a customized version of the touchscreen in a vertical orientation.
“In terms of branding, the HMIs look sleek and modern,” Lalande says. “The nicer appearance and intuitive operation create better first impressions and user experience for customers, which goes a long way.”
3D Printer Motion Control and Safety with EtherCAT and Servo Technologies
Meld’s L3, K2 and 3PO machines rely on Beckhoff servo solutions for motion control. A variety of AX5000 servodrives and AM8000 servomotors with appropriate gearboxes handle movement in X, Y and Z coordinates. DIN-rail-mounted EL72xx servodrive terminals power a continuous feeding system for the barstock that Meld’s process consumes.
“The feeding system allows operators to load eight hours’ worth of material at once,” Lalande explains. “The material automatically moves to the turret as needed using Beckhoff compact motion solutions.” The Beckhoff components also offer One Cable Technology (OCT), which combines power and feedback in one cable to simplify commissioning.
Beyond real-time communication, flexible topology and simple interfacing to other common protocols, a major benefit of the EtherCAT industrial Ethernet system has been its plug-and-play ease, according to Lalande, when using devices from Beckhoff as well as from third parties. Each machine’s rotating deposition tool is driven by a VFD and spindle motor from a third party, but because the VFD is EtherCAT-based, integration has been simple, he says.
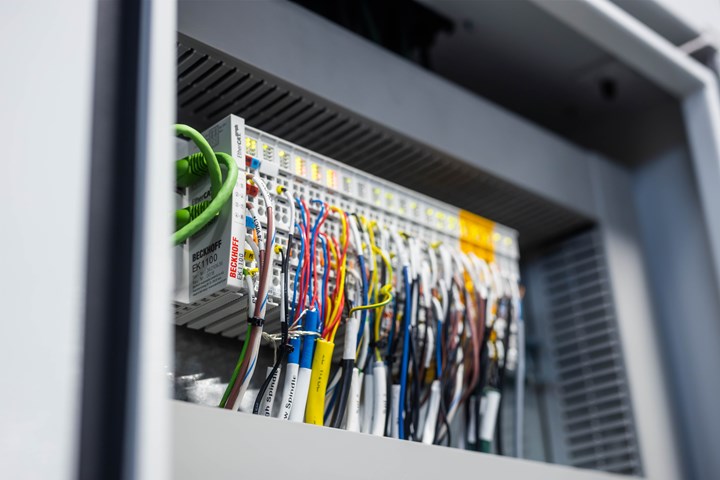
Meld machines use a variety of EtherCAT I/O and TwinSafe functional safety terminals. Photo Credit: Beckhoff / Foreword LLC
Meld also leverages Beckhoff’s TwinSafe integrated functional safety solution. With its black channel approach, TwinSafe uses the Safety over EtherCAT (FSoE) protocol to send safety data over the same Ethernet cables as standard communication. This allows Lalande to implement E-stops, safety doors and TwinSafe motion functions for the drives with programming in the same TwinCAT engineering environment.
3D Printing Grows With Futureproof Technologies
As Meld continues to make advances in additive manufacturing, PC-based control provides a solid foundation to build upon. EtherCAT and OCT shorten commissioning times, while TwinCAT consolidates HMI, motion control, PLC and other machine control functions into one universal software. The automation platform also simplifies the implementation of OPC UA, LabVIEW, MATLAB/Simulink or other software tools as needed in the future, depending on customer specifications or developments.
To keep pace with Meld’s innovation, TwinCAT provides development tools that help maintain a uniform code base across the machines. Seamless integration of source control tools, such as Git, into TwinCAT engineering and the TwinCAT Project Compare Tool are just two advantages. “Managing our beta testing is made easier with these tools,” Lalande says.
“With reliable automation technologies as a base, we continue to refine our capabilities and add exciting new solutions,” Cox says. “For example, the Jointless Hull project machine is very big — the largest of its kind so far — but it's not the biggest machine we are working on with customers right now.”
Related Content
Ultimaker 5.0 Cura Enables Finer, Faster Prints
The software’s enhanced slicing engine is said to enable thinner walls and finer details in additive manufacturing.
Read MoreTo Scale Additive Manufacturing, Separate Design and Production
Spokbee’s online marketplace is designed to ease the launch and sale of customizable, 3D printed products. Its flexibility comes from cloud-based CAD and a distributed network of service bureaus for production.
Read MoreActivArmor Casts and Splints Are Shifting to Point-of-Care 3D Printing
ActivArmor offers individualized, 3D printed casts and splints for various diagnoses. The company is in the process of shifting to point-of-care printing and aims to promote positive healing outcomes and improved hygienics with customized support devices.
Read MoreAdditive Manufacturing Production at Scale Reveals the Technology's Next Challenges: AM Radio #28
Seemingly small issues in 3D printing are becoming larger problems that need solutions as manufacturers advance into ongoing production and higher quantities with AM. Stephanie Hendrixson and Peter Zelinski discuss 6 of these challenges on AM Radio.
Read MoreRead Next
How a Solid-State Process Stood Firm Until Additive’s Moment
Early on, this company saw the promise of friction stir welding for building forms in layers. Few understood at the time. They understand now, in part because this process offers benefits such as blended materials and freedom from stress that other metal AM approaches can’t match.
Read More3D Printing From Barstock Using Friction Stir Welding (Video)
A look at the Meld Manufacturing metal AM process. The machine tool in this video builds an additively manufactured part by rotating and compressing metal bar.
Read MoreHybrid Additive Manufacturing Machine Tools Continue to Make Gains (Includes Video)
The hybrid machine tool is an idea that continues to advance. Two important developments of recent years expand the possibilities for this platform.
Read More